- RISACORPS ABB
- RISACORPS PANASONIC
- Panasonic PLC
- Panasonic Servo
- Panasonic HMI
- AC Geared Motor
- Panasonic FA Component
- Panasonic Limit Switch
- Panasonic Sensor
- Panasonic Image Checker
- Panasonic Laser Marker
- Panasonic UV Curing System
- Panasonic Power Meter
- Pre-Order Products (1-3 Months)
- Discontinued Panasonic Products (Call for Stock Availability)
- RISACORPS HITACHI
- RISACORPS MEAN WELL
- RISACORPS NIDEC SHIMPO
- RISACORPS KSS
- RISACORPS WEIDMULLER
- RISACORPS WEINTEK
- RISACORPS MAX LETATWIN
- RISACORPS TOGAMI
- RISACORPS SIKES
- RISACORPS MICNO
Müller Dairy meningkatkan efisiensi produksi melalui otomasi dengan ABB
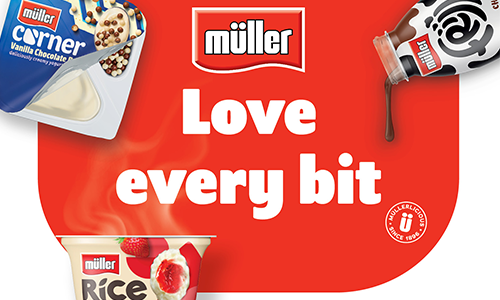
Müller Berinvestasi dalam Otomasi
Müller Dairy, sebuah kisah sukses Eropa dalam inovasi produk dan pengembangan merek, kini menjadi produsen yogurt terbesar di Inggris. Beroperasi dari kantor pusatnya di Market Drayton, bisnis ini terus berkembang dengan kapasitas produksi mencapai dua miliar pot per tahun. Tekanan untuk meningkatkan output, mengurangi biaya, dan meningkatkan fleksibilitas produksi terus berlanjut untuk memenuhi permintaan saat ini serta mengembangkan peluang baru.
Tantangan yang Dihadapi
Müller Dairy menyadari bahwa kemampuan manufakturnya dapat ditingkatkan secara signifikan dengan melakukan peningkatan dan rekayasa ulang pada lini repack yang ada. Lini tersebut terlalu bergantung pada intervensi manual dan kinerjanya kurang optimal. Selain itu, sistem ini kurang fleksibel karena awalnya tidak dirancang untuk menangani pot kembar, padahal segmen ini menjadi area pertumbuhan utama bisnis.
Solusi yang Diterapkan
Müller Dairy menunjuk CKF Systems dari Gloucester sebagai mitra proyeknya, dengan tanggung jawab untuk merancang, menginstal, dan melakukan komisioning solusi otomatis sepenuhnya. Proyek ini memanfaatkan banyak peralatan yang sudah ada dan tetap berada dalam ruang lantai yang sama.
Empat robot ABB Flexpicker menjadi inti sistem yang telah ada. Insinyur Proyek Müller, Martyn Steadman, meminta ABB merekomendasikan integrator sistem yang mampu menangani tantangan kompleks, termasuk keterbatasan ketinggian di lokasi lantai dasar.
“Dari daftar pendek empat kandidat, kami memilih CKF karena mereka sejalan dengan cara berpikir kami sejak awal diskusi,” kata Steadman. “Kami terkesan dengan ide-ide mereka, hubungan pelanggan, serta kualitas dan kinerja proyek-proyek mereka sebelumnya.”
Proyek ini merupakan investasi besar bagi Müller Dairy dan menuntut pengembalian yang cepat. Solusi yang diterapkan harus inovatif dan terintegrasi dalam ruang yang terbatas. Untuk memaksimalkan output, konfigurasi yang ada harus direkayasa ulang guna menghilangkan hambatan produksi, memasang motor dan perangkat lunak baru, serta memperkenalkan protokol konveyor inovatif untuk memastikan penyelarasan produk yang akurat guna penanganan berkecepatan tinggi.
Penting agar sistem baru ini dapat segera beroperasi dengan gangguan minimal pada produksi yang sedang berjalan. Sejalan dengan tujuan strategis Müller Dairy, pekerjaan ini harus dilakukan dengan standar tertinggi dan dalam kerangka keselamatan yang ketat.
Robot ABB Flexpicker menjadi bagian integral dari solusi ini, menangani repack yogurt ke dalam format multipack dengan kapasitas 420 pot per menit. CKF Systems sangat senang terpilih untuk proyek yang menantang ini, dan sebagai ABB Authorized Value Provider, CKF memberikan kepercayaan lebih kepada pelanggan.
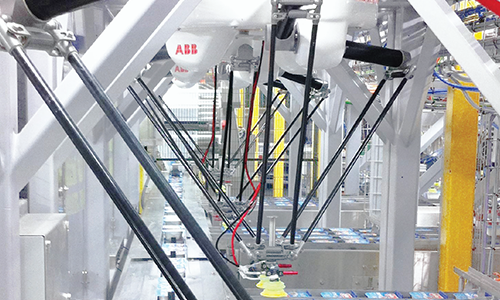
Cara Kerja Sistem Baru
Persyaratan fungsional sistem repack ini adalah mengambil yogurt yang sudah dikemas dari palet, membuat multipack, mengemas ulang, dan mempaletkan kembali.
Sistem yang dirancang CKF memiliki empat jalur masuk untuk menangani multipack dengan berbagai rasa. Setiap jalur mengumpulkan baki bertumpuk yang kemudian diurai sebelum sistem pemindahan gantry mengambil yogurt dari baki tersebut. Yogurt kemudian ditempatkan di konveyor masukan Flexpicker, yang mengarahkan setiap pot ke posisi yang diinginkan. Baki kosong kemudian dipindahkan ke jalur untuk digunakan kembali pada proses pengepakan.
Empat Flexpicker mengikuti jalur konveyor masuk dan jalur masukan pembungkus aliran (flow wrapper), memilih jumlah pot yang dibutuhkan dan menempatkannya dalam setiap unit pengemasan. Setelah dikemas dengan pembungkus aliran, multipack diputar 90 derajat, dikumpulkan dalam sistem pengepakan, dan kemudian ditempatkan kembali ke dalam baki awal.
Tantangan dan Solusi
“Tantangan proyek ini dan potensi kendalanya sangat besar,” jelas Kevin Staines, Direktur Penjualan CKF Systems Ltd. “Kami awalnya melakukan serangkaian uji coba di pabrik kami di Gloucester untuk membuktikan solusi yang diusulkan. Setelah itu, kami melakukan pengujian penerimaan pabrik penuh. Dengan cara ini, kami dapat menghilangkan semua risiko dan memastikan pemasangan serta komisioning sistem dengan gangguan minimal.”
Kondisi lingkungan juga berdampak pada kinerja sistem. Dalam situasi ini, bekerja di area pendingin dengan suhu konstan yang rendah membutuhkan pertimbangan tambahan, seperti kinerja cengkraman vakum.

Hasil dan Manfaat
Dari perjanjian kontrak hingga penyelesaian, investasi ini dilakukan dalam waktu kurang dari delapan bulan, dengan manfaat langsung bagi bisnis.
Kini, lini repack yang sepenuhnya otomatis menjadi setidaknya 50% lebih efisien dan mampu menangani dua kali lipat jumlah yang sebelumnya dilakukan secara manual.
“Ini adalah proyek yang menantang namun sangat menarik,” lanjut Martyn Steadman. “Solusi ini memenuhi semua harapan investasi kami dan tujuan strategis Müller Dairy untuk menjadi perusahaan susu paling kompetitif dan sukses di Inggris dan Irlandia.”
Selain itu, proyek ini membawa manfaat dalam aspek kesehatan dan keselamatan kerja. Dengan mengurangi proses kerja berulang berkecepatan tinggi dalam ruang terbatas, pekerja dapat dialihkan ke tugas yang lebih produktif. Sistem baru ini juga lebih mudah dibersihkan, memerlukan lebih sedikit perawatan, serta dirancang untuk kemudahan penggunaan dan akses.
Proyek ini telah disetujui oleh Tim Teknis Pusat di Aretsried, Jerman, dan menjadi tolok ukur baru dalam hal desain, implementasi, inovasi, serta kinerja investasi di masa depan.
Sumber: Dairy ABB Muller Casestudy